Heineken, Worldwide
Raising the bar for international breweries
An independent brewer since 1864, Heineken is currently Europe’s number 1 and the world’s number 2 beer producer. The Amsterdam original has become a global player, sold in more than 170 countries, with a portfolio of over 200 regional and local brands, making Heineken the world’s most international premium beer brand.
The project
In the last few decades, the beer industry has evolved rapidly, driven by the ever-growing market demands, but also the health and safety requirements for customers and end users. Moving away from brass compression fittings traditionally used for carrying beer in the late 1980s, due to health concerns over lead reacting with beverages, the industry has seen a number of improvements in the way beer is stored and dispensed at a bar or a restaurant.
Heineken decided to raise hygiene standards even further and eliminate the risk of any microbiological activity in the beer line by keeping it consistently cool. The Dutch brewer needed a partner who has been living and breathing the drinks dispense industry long enough to accommodate their high-quality requirements, which is where RWC’s plastic push-to-connect trendsetter John Guest came along.
RWC’s involvement
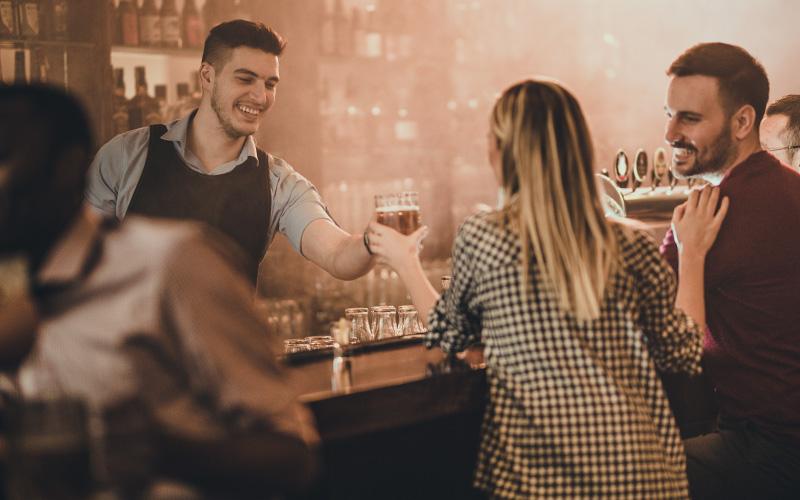
Introducing the world’s first food grade plastic push-to-connect fitting in the 1980s, RWC’s John Guest has been instrumental in the transformation of a number of industries, including beer and drinks dispense.
With such expertise and always keen to be at the forefront of innovation, JG collaborated with Heineken to develop a connector to bring extra cold beer straight from the keg to the font. Known as PolarClean, the tube-in-tube connector keeps beer lines consistently cool at brand specification temperatures, eradicating the risk of any microbiological activity, while improving carbonation control and reducing product waste.
Carrying beverages through a tube encased by another tube with coolant, the connector delivers perfectly chilled beer from the keg coupler to the beer tap without the necessity of a cold room or a secondary cooling device.
Project at a glance
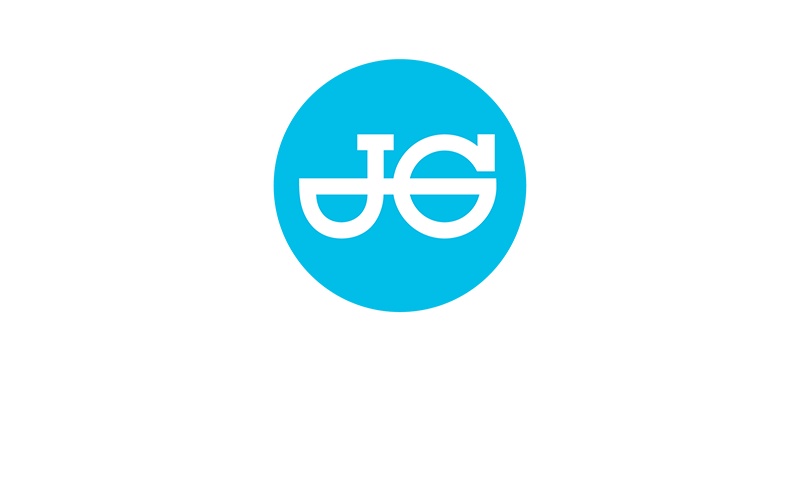
Development: Tube-in-tube cooling technology
Client: Heineken, UK
Requirement: Consistent beer temperature at pour; reduced beer line microbiological activity.
Specified solution: John Guest PolarClean